MODELLING AND SIMULATION OF AN MR BRAKE BASED ON TORQUE COMPENSATION
DOI:
https://doi.org/10.11113/jtse.v11.214Keywords:
Brake-by-wire system, reverse extrusion, magnetorheological brake, temperature compensation, electromagnetic field simulationAbstract
A new design for a repetitive compression magnetorheological (MR) brake has been introduced, aiming to enhance both the efficiency and safety of vehicle safety systems, thereby accelerating the commercial adoption of such brakes in the automotive industry. This innovative brake uses a hybrid operational mode, replacing the conventional rotary motion with a unique recessive structure to enhance the braking performance. In the non-braking state, the design maintains the fluidity of the MR fluid, while in the braking state, it leverages the brake disc's recessive movement. Additionally, the study incorporates a temperature compensation mechanism to mitigate potential performance variations due to temperature changes. A three-dimensional static magnetic field analysis confirmed the magnetic circuit design's effectiveness and the suitability of the selected parameters and materials. The simulation showed that the brake's average magnetic field intensity rose by 145.26% when increasing the current from 1A to 4A, achieving a maximum braking torque of 51.4 Nm.
References
Wang D. M., Yang G. X., Luo Y. J., Fang S. R., Dong T., (2023). Optimal design and stability control of an automotive magnetorheological brake considering the temperature effect. Smart Materials and Structures. 32(2): 025020. https://dx.doi.org/10.1088/1361-665X/acb1e2.
Shamieh H., Sedaghati R., (2018). Development, optimization, and control of a novel magnetorheological brake with no zero-field viscous torque for automotive applications. Smart Materials and Structures. 29(16): 3199-213. https://dx.doi.org/10.1088/1361-665X/aa9452.
Patil S. R., Sawant S. M., (2018). Experimental Studies on Magnetorheological Brake for Automotive Application. Int. J. Automot. Mech. Eng. 15(1): 4893-908. https://dx.doi.org/10.15282/ijame.15.1.2018.2.0381.
Kalikate S. M., Patil S. R, Sawant S. M., (2018). Simulation-based estimation of an automotive magnetorheological brake system performance. Journal of Advanced Research. 14: 43-51. https://dx.doi.org/10.1016/j.jare.2018.05.011.
Shamieh H., Sedaghati R., (2017). Multi-objective design optimization and control of magnetorheological fluid brakes for automotive applications. Smart Materials and Structures. 26(12): 125012. https://dx.doi.org/10.1088/1361-665X/aa9452.
Wu J., Deng B., Huang Y., Zhang H., Tang S., (2022). A multi-pole magnetorheological clutch powered by permanent magnets and excitation coils. Journal of Intelligent Material Systems and Structures. 34(2): 217-28. https://doi.org/10.3390/act11050120.
Singh R. K., Sarkar C., (2023). Two-wheeler magnetorheological drum brake operating under hybrid mode for enhancing braking torque: Development and validation. Mechatronics. 92: 102971. https://dx.doi.org/10.1016/j.mechatronics.2023.102971.
Thakur M. K., Sarkar C., (2021). Investigation of Different Groove Profile Effects on Torque Transmission in Shear Mode Magnetorheological Clutch: Numerical Simulation and Experimental Study. Journal of Tribology. 143(9): 091801. https://dx.doi.org/10.1115/1.4049255.
Nguyen V. B., Le H. D., Nguyen QH, Duyen DQ, Hieu DHM, Choi S-b., (2021). Design and experimental evaluation of a novel magneto-rheological brake with tooth-shaped rotor. Smart Materials and Structures. 31(1): 015015. https://dx.doi.org/10.1088/1361-665X/ac38ff.
Ye F., Peng D., Yuan Y., Wang X., Qing O., (2020). Multi-objective optimization design and performance evaluation of T-shaped magnetorheological brake. Journal of Simulation. 8(4): 88-91. https://doi.org/10.3390/act11050120.
Nguyen Q. H., Nguyen V. B., Le H. D., Duyen D. Q., Li W., Hung N. X., (2021). Development of a novel magnetorheological brake with zigzag magnetic flux path. Smart Materials and Structures. 30(12): 125028. https://dx.doi.org/10.1088/1361-665X/ac3430.
Shiao Y. J, Kantipudi M. B., (2021). High torque density magnetorheological brake with multipole dual disc construction. Smart Materials and Structures. 31(4) 045022. https://dx.doi.org/10.1088/1361-665X/ac5860.
Chen W., Xiong Y., Shu R., Huang J., (2022). Analysis and experimentation of an adjustable gap magnetorheological brake controlled by electrothermal shape memory alloy spring. Journal of the Brazilian Society of Mechanical Sciences and Engineering. 44(8): 358. https://dx.doi.org/10.1007/s40430-022-03657-x.
Bazargan-Lari Y., (2019). Design and shape optimization of MR brakes using Nelder–Mead optimization algorithm. Mechanics & Industry. 20(6): 602. https://dx.doi.org/10.1051/meca/20190
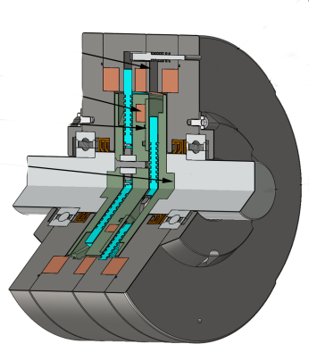
Downloads
Published
How to Cite
Issue
Section
License
Copyright of articles that appear in Journal of Transpot System Engineering (JTSE) belongs exclusively to Penerbit Universiti Teknologi Malaysia (Penerbit UTM Press). This copyright covers the rights to reproduce the article, including reprints, electronic reproductions or any other reproductions of similar nature.
Disclaimer: The views and opinions expressed in the articles are those of the authors and do not necessarily reflect the official policy or position of the JTSE. Examples of analysis performed within are only examples and they should not be utilized in real-world. Assumptions made within the analysis are not reflective of the position of any JTSE entities.